
“The AI-based PPE Monitoring System from The Disrupt Labs has transformed our approach to workplace safety. Automating PPE monitoring has minimized human error, brought compliance levels to over 95%, and saved us countless hours previously spent on manual tracking. The system’s intuitive dashboard and automated reporting allow our management team to make informed, data-driven decisions, significantly boosting both safety and operational efficiency. It has truly set a new benchmark for safety at our facility.”
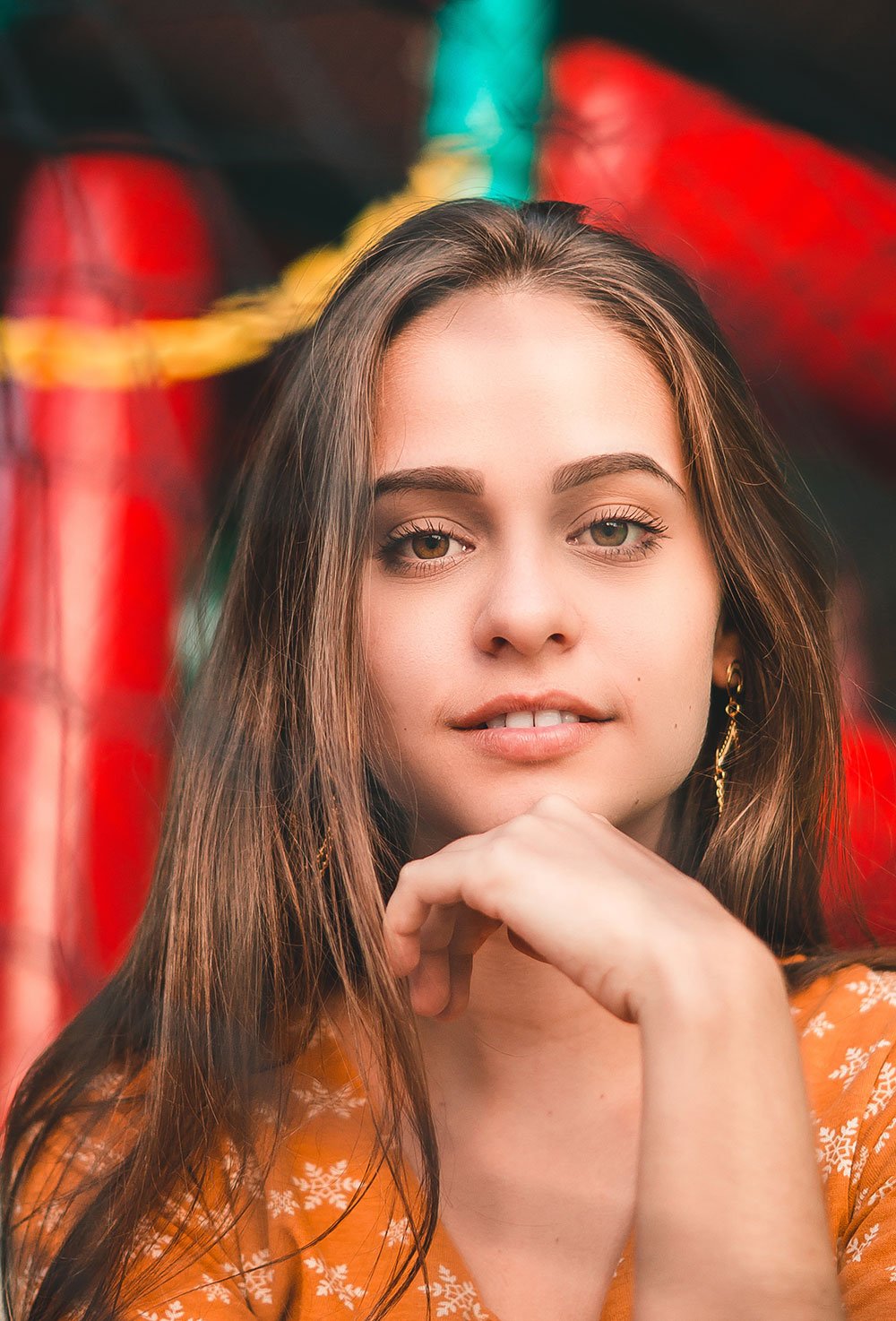
M/S Axens
Representative