Occupational Health and Safety Standard Operating Procedures (SOPs) for a Safer Workplace
Why Occupational Health and Safety Matters?
Occupational Health and Safety focuses on protecting employees from accidents, injuries, or exposure to harmful elements. In today’s regulatory landscape, this responsibility goes hand-in-hand with effective EHS Compliance Management, which is a structured approach to ensuring that environmental, health, and safety standards are consistently met.
In workplaces, it is the responsibility of employers to ensure that certain measures are taken to reduce the risk of incidents and create a safe working environment for all employees. A healthy and secure work environment leads to fewer accidents, boosted employee morale, and enhanced productivity.
What are Standard Operating Procedures (SOPs)?
Standard Operating Procedures (SOPs) are detailed, step-by-step written instructions on how to perform or execute a certain work procedure. Organizations follow Standard Operating Procedures (SOPs) to maintain consistency and adhere to compliance or regulatory standards for their business operations. The main purpose of Occupational Health and Safety Standard Operating Procedures (SOPs) is to protect employees, customers, and all individuals from the hazards and risks of the workplace.
How do Standard Operating Procedures (SOPs) Improve Workplace Safety?
Implementing Standard Operating Procedures SOPs in the workplace significantly enhances safety and creates a safe environment for the employees. Prioritizing SOPs improves workplace safety by:
- Reducing human error: Clear and detailed step-by-step instructions minimize mistakes made by humans, which can cause accidents or injuries.
- Standardizing safe practices: Tasks performed by the employees use the same safe methods every single time to ensure uniformity within the tasks.
- Improving Hazard Awareness: SOPs help identify potential risks and then offer effective measures to mitigate them.
- Enhancing Training: Standard Operating Procedures also serve as key tools for training and development, especially for newer employees or for high-risk job roles.
- Providing Emergency Guidance: In emergencies, SOPs offer step-by-step guidance and assistance that can essentially save multiple lives.
These procedures embed a safety-first mindset into daily routines, making them an essential workplace safety topic in every organization.
Occupational Safety and Health Administration (OSHA)’s Influence on Workplace Safety Standards
The Occupational Safety and Health Administration (OSHA), established in 1970 under the U.S. Department of Labor, remains one of the most influential forces in shaping workplace safety. OSHA develops comprehensive health and safety standards that ultimately serve as the foundation for organizations to build their occupational health and safety standard operating procedures.
These standards are a legal compliance and are specifically tailored to different industries and different job functions. These standards guide how tasks are performed safely, what equipment must be used, and what controls must be in place to protect employees from harm.
Some of the most commonly integrated OSHA standards in SOPs include:
- Personal Protective Equipment (PPE): OSHA specifies when PPE is required, how it should be worn, maintained, and inspected. This includes safety helmets, gloves, masks, vests, eye protection, and respiratory gear.
- Hazard Communication: This standard requires employers to accurately communicate the details of hazardous chemicals through labelling, safety data sheets, and proper training of employees.
- Fall Protection: OSHA specifies the specific conditions under which fall protection systems like harnesses and guardrails must be used.
- Machine Guarding: This requires physical barriers and operational controls to prevent contact with dangerous machine parts.
- Emergency Action Plans (EAPs): Outlines requirements for evacuation routes, alarm systems, and staff responsibilities in case of fire, chemical spills, or other emergencies.
These standards are not merely guidelines; they directly shape the structure and content of workplace SOPs.
Today, organizations recognize that compliance isn’t just about avoiding penalties; it’s about building smarter, safer, and healthier worksites. The Disrupt Labs contributes to this evolution by exploring innovative ways to merge technology, training, and safety policies, therefore, ensuring that SOPs remain dynamic, data-driven, and future-ready. The Disrupt Labs integrates AI Computer Vision in Environmental, Health and Safety (EHS) Compliance Management to ensure that workplaces are safer in real-time.
Key Elements of Effective Standard Operating Procedures (SOPs)
Every organization should tailor its occupational health and safety standard operating procedures based on its unique needs. However, effective SOPs typically include the following:
- Clear Purpose or Scope
Every SOP should begin with the reason behind why it exists and who it refers to or applies to. This section of Occupational Health and Safety Standard Operating Procedures (SOPs) outlines the objective of the procedure and the roles, departments, or environments it covers. A clearly stated purpose and scope ensure that every individual understands the importance of following these safety goals and their relevance to the daily operating tasks.
- Step-by-Step Procedures
This section on an SOP provides step-by-step, extensive details for executing tasks safely. Each step is written in clear, actionable language so that there is no ambiguity in understanding the text. In some situations, visuals like diagrams are also used to enhance comprehension.
- Safety Controls and PPE Requirements
A well-developed SOP will always include instructions on all necessary safety measures, including Personal Protective Equipment (PPE), hazard controls, and risk-reduction strategies. This Section ensures that all personnel are well-equipped and protected before any task begins.
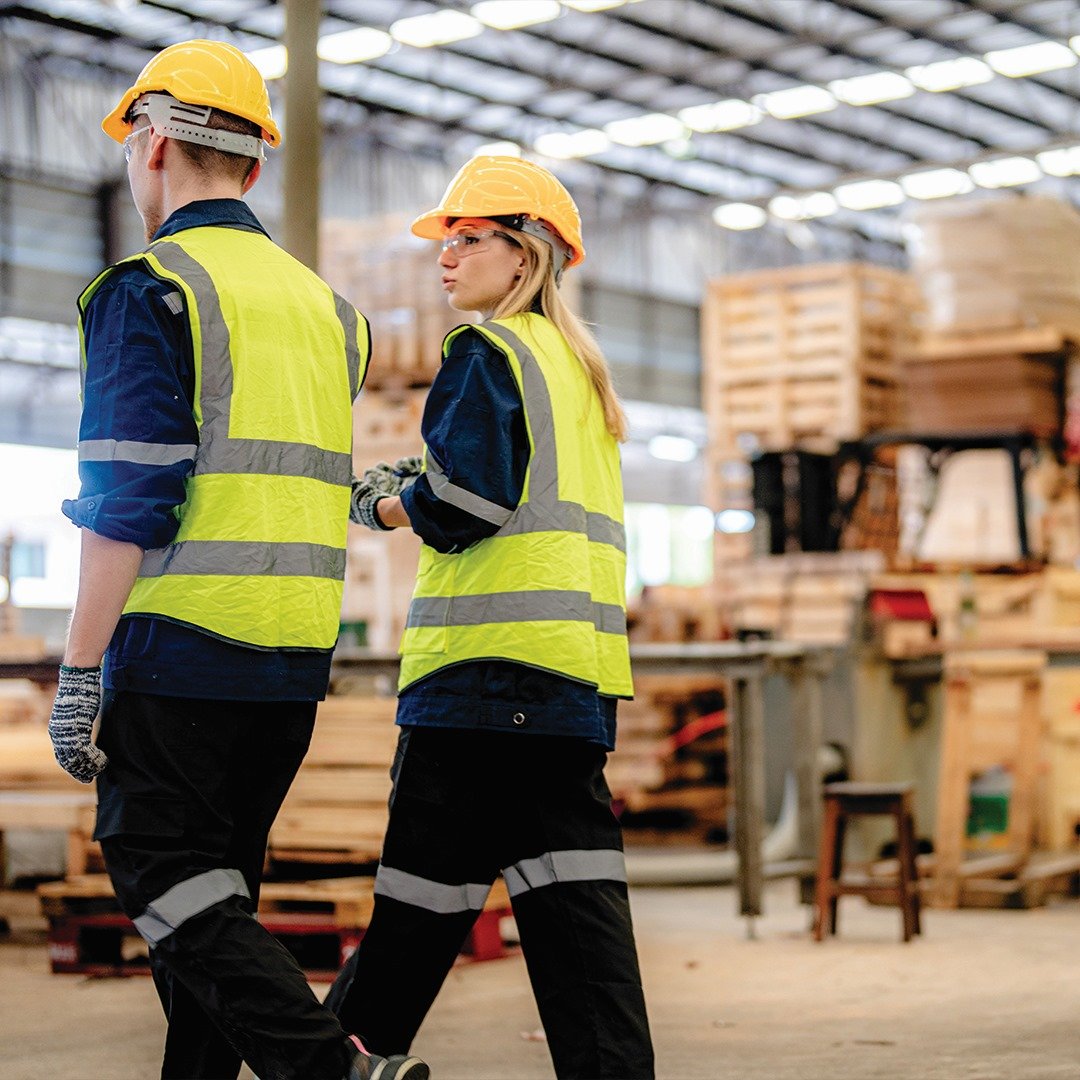
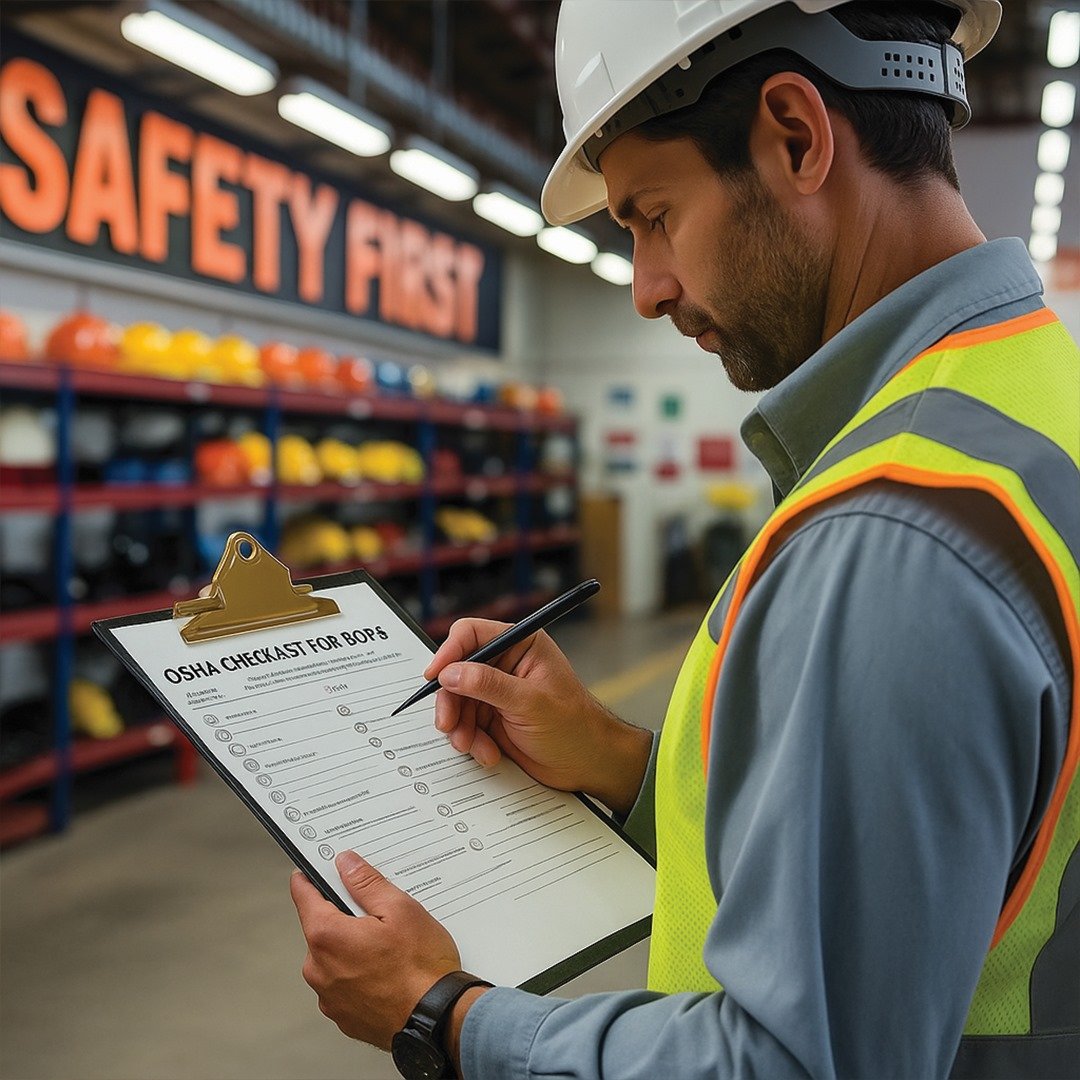
- Emergency Protocols
Incidents can occur, even when all necessary safety measures have been taken. This is why SOPs also clearly design an emergency response plan. This plan includes the steps and actions that need to be taken in case of different emergencies, such as accidents, spills, equipment failures, fires, or medical emergencies.
- Training Requirements
Employees need proper training to carry out procedures safely. This section outlines the type and frequency of training required, any certifications needed, and who delivers the training. Ongoing education helps reinforce SOPs and ensures teams remain competent and confident in their roles.
- Documentation and Record Keeping
This part lists any supporting documents, forms, or logs that must be maintained, such as inspection sheets, maintenance records, or hazard assessments. These documents help verify compliance and provide data for continuous improvement.
- Review, Approval, and Revision History
To remain effective, safety SOPs must evolve. This section includes details of the SOP’s approval, version history, and scheduled review dates.
Conclusion
Occupational health and safety standard operating procedures bring structure to complex operations, align teams with legal and ethical standards, and empower employees to act confidently and responsibly.
By aligning your SOPs with the Occupational Safety and Health Administration (OSHA) regulations and evolving industry standards, you not only reduce incidents but also develop a more motivated and high-performing workplace.
At The Disrupt Labs, we’re committed to helping businesses evolve their safety strategies with data-driven insights and modern AI industrial safety solutions.
Ready to take the next step toward a safer, smarter workplace? Contact us today.
Frequently Asked Questions
Occupational Health and Safety SOPs are structured documents that outline step-by-step instructions for performing tasks safely. They help ensure EHS compliance, reduce risk, and promote consistency in workplace safety practices.
SOPs improve workplace safety by standardizing procedures, minimizing human error, ensuring compliance with regulations, and training employees effectively in safe work practices.
The Occupational Safety and Health Administration (OSHA) sets mandatory standards that help create health and safety SOPs. These standards guide everything from PPE use to emergency response protocols.
Computer Vision AI can continuously monitor workplace activities, detect violations, and alert safety managers, ensuring compliance with OSHA regulations.